In January, Volkswagen announced that the solid-state battery products from QuantumScape (QS), an American battery manufacturer, had passed an endurance test conducted by PowerCo, a battery-focused subsidiary of Volkswagen. Following the announcement, the stock price of QS surged by over 40% in a single day.
Just a month prior to the milestone achieved by QS, William Li (also known as Li Bin), CEO of Nio, had also drawn widespread attention after driving for 12.4 hours in the cold winter to test the 1,000-kilometer range of the semi-solid-state battery pack installed in Nio’s ET7 electric vehicle model. Li later claimed on Weibo that this is currently the “battery with the highest energy density in mass production globally.”
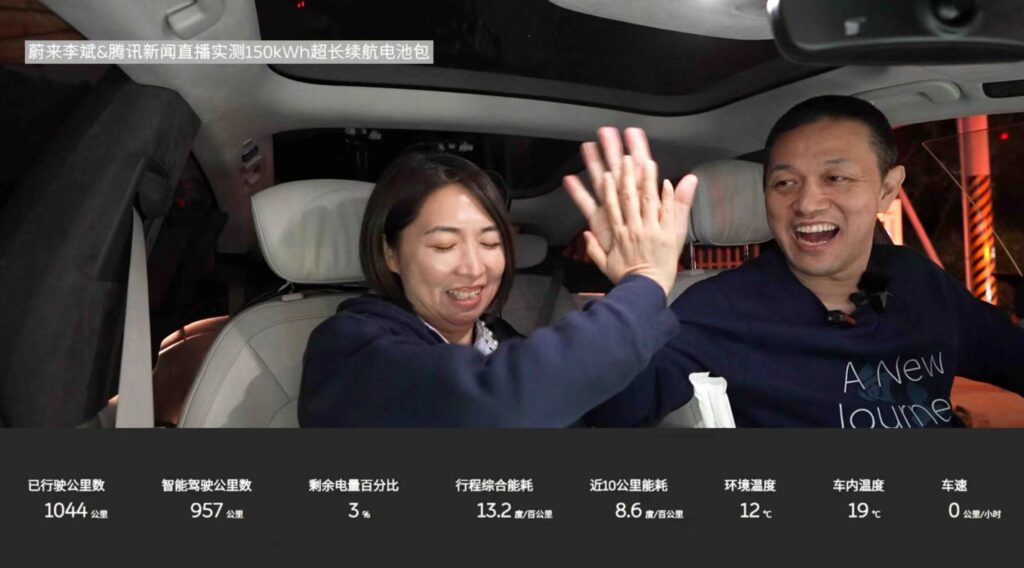
Solid-state batteries have increasingly been referred to as the “ultimate form of lithium batteries” within the industry. Compared to the current mainstream liquid-based batteries, they offer significant advantages in terms of energy density, safety, charging rates, and cycle life. Thus, industry participants have proclaimed at times that “the day solid-state batteries become mainstream is the day gasoline cars exit the stage of history.”
However, in the current scenario where liquid batteries are approaching performance limits and facing overcapacity, automakers have been pursuing new developments in solid-state batteries, becoming a major point of discussion and speculation among market observers.
What is less clear within the market are two significant different paths in the development of battery technology. On one hand, there are semi-solid-state batteries that are nearly ready for mass production and commercialization in verticals such as drones, energy storage, and new energy vehicles. On the other hand, solid-state batteries are ostensibly still in their infancy, with the prospect of being integrated into vehicles remaining distant.
Yet, both battery types face a similar dilemma: the high cost that makes it challenging to penetrate downstream markets, especially as liquid batteries become increasingly affordable. Even semi-solid-state batteries, which are more mature in development and have increasingly obvious use cases, have seen adoption held back by their high prices.
Several years ago, high-density batteries were an unreachable luxury for manufacturers and consumers alike. In 2015, Volkswagen predicted that the application of solid-state battery technology could potentially increase the range of EVs to 700 kilometers. However, this prediction has proven to be overly conservative. Today, improvements in battery structure have enabled lithium iron phosphate (LFP) batteries to achieve ranges of up to 700 kilometers. Moreover, semi-solid-state batteries with a 1000-kilometer range are now a reality and capable of being mass-produced.
When Li drove the ET7, which was equipped with a 150 kWh semi-solid-state battery pack, he was said to have achieved a range of 1,044 kilometers. This battery pack was developed by WeLion New Energy Technology, with technical and financial support provided by Nio. Li has previously told various media outlets that the production capacity of this battery is ramping up and will commence deliveries soon.
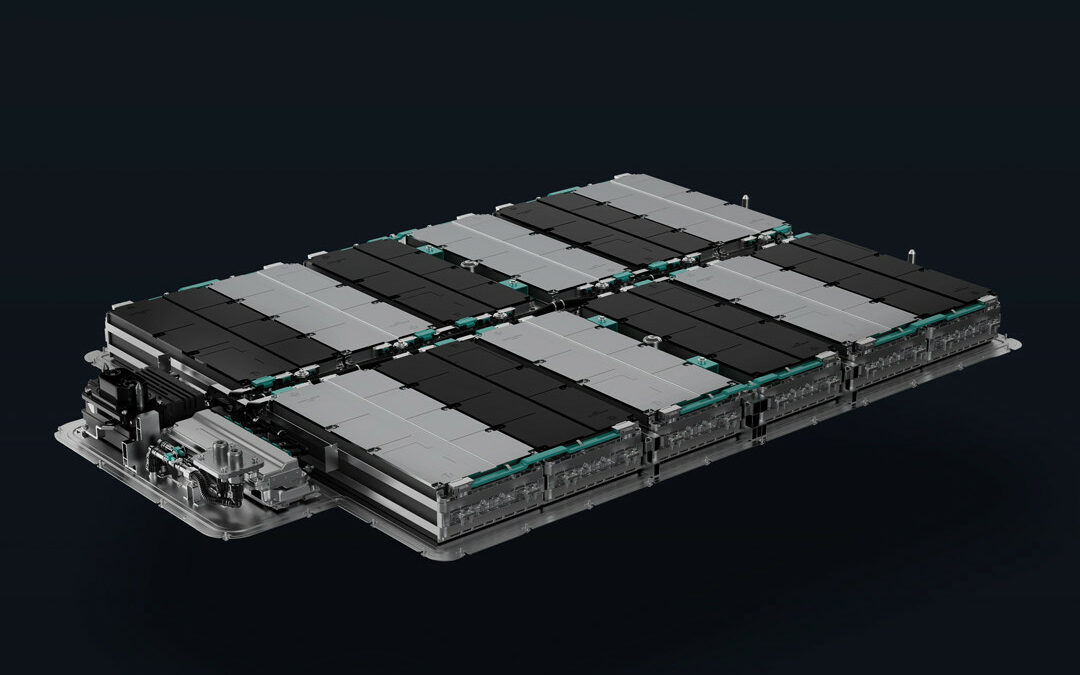
Nio is not the first automaker to integrate semi-solid-state batteries into vehicles. Since 2023, companies such as Dongfeng Motor, Zeekr, and Seres have also implemented semi-solid-state batteries in their vehicles, with some already in delivery.
According to data compiled by ICC, the annual installation volume of solid-state and semi-solid-state batteries in China in 2023 was approximately 0.6 GWh, with core supplies mainly coming from WeLion, Farasis Energy, and Ganfeng Lithium, among which WeLion contributed around 0.4–0.5 GWh.
In addition to new energy vehicles, semi-solid-state batteries have been utilized for commercial applications in niche verticals such as drones. WeLion, for instance, started mass-producing semi-solid-state batteries for drone products as early as 2020, supplying more than 50 companies.
In the energy storage market, portable energy storage and household energy storage systems have experimented with semi-solid-state batteries, with various projects in large-scale energy storage underway. HyperStrong Technology, for instance, has deployed semi-solid state battery systems for two pilot projects. Zendure launched household energy storage products equipped with semi-solid-state batteries in 2022, with Xiaomi, ETaker, and Qianson Power launching outdoor equivalents the same year.
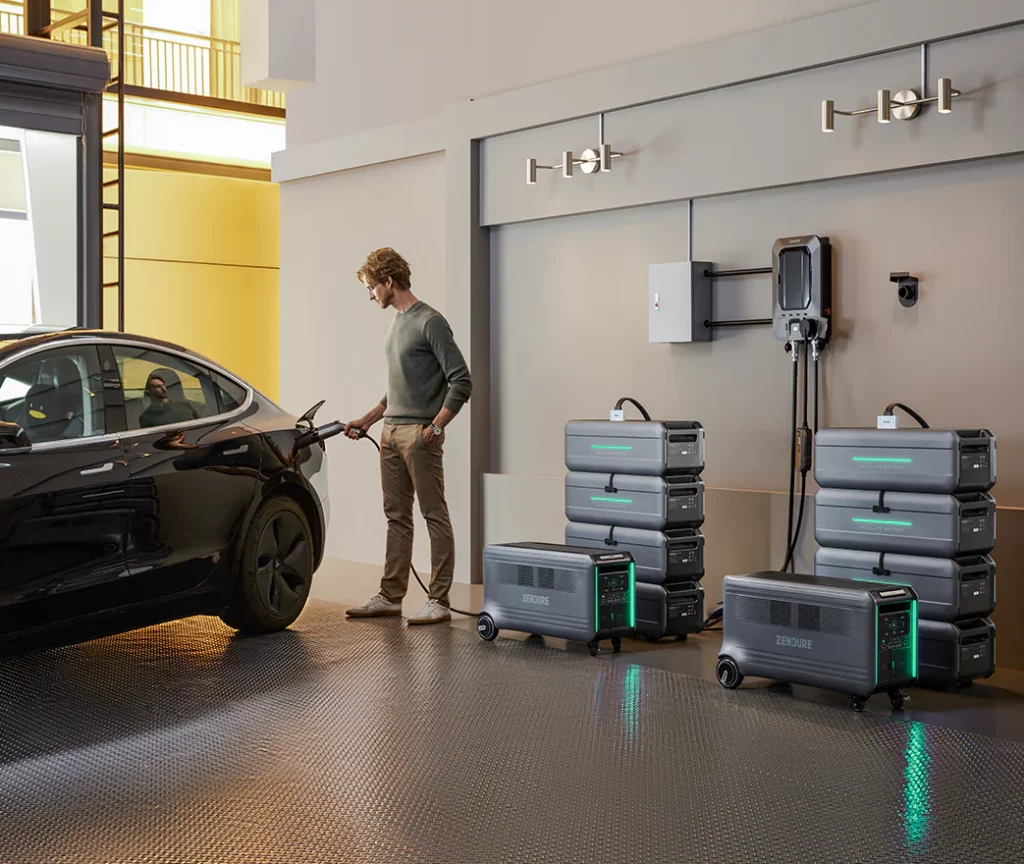
According to Wang Xin, founder of REnergy Tech, the use cases for semi-solid-state batteries are becoming increasingly clear, evident in companies receiving orders for delivery on the consumer side.
In 2024, semi-solid-state batteries are anticipated to experience a ramp-up in production capacity amidst a rise in market demand. Automakers such as SAIC Motors and GAC have announced their sales plans for semi-solid-state battery models this year, and Contemporary Amperex Technology (CATL) has also stated its intention to promote the application of its condensed solid-state battery (with an energy density of 500 Wh/kg) in vehicles in 2024.
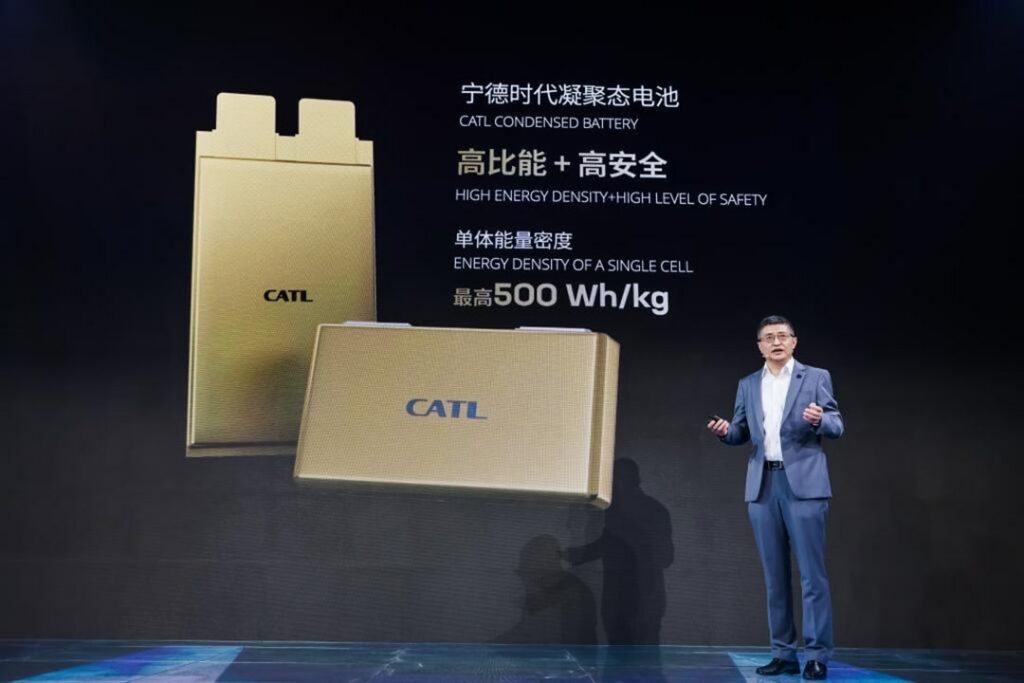
According to research firm GGII, over five new vehicle models equipped with semi-solid-state batteries will be launched and sold in the Chinese market this year, with total sales estimated to exceed 5 GWh.
However, price remains a barrier to adoption. The 150 kWh battery pack equipped in the ET7 has a capacity at least 50% higher than most EV battery packs, but its cost has more than doubled, reaching nearly RMB 300,000 (USD 42,230). Due to the hefty cost, Nio has temporarily decided not to sell it but rent the battery on a daily basis instead. Outdoor power products equipped with semi-solid-state batteries, such as Xiaomi’s Mijia 1,000 Pro and Qianson Power’s QX3600, are also priced over 50% higher (per watt-hour) compared to regular alternatives.
Price is, therefore, a clear factor that limits the scope and scale of semi-solid-state batteries in downstream markets. Currently, besides drones, such batteries remain unable to penetrate the market in verticals such as energy storage and new energy vehicles. Companies that lead in these fields seemingly still prefer more affordable and technologically mature liquid, lithium-based batteries.
Citing an unnamed industry investor, 36Kr said that semi-solid-state batteries utilizing silicon-based negative electrodes are mainstream in China, as their bill of materials (BOMs) and overall costs are not significantly different from liquid batteries. The low yield of production lines has the most significant impact on costs—by improving the yield of production lines, the cost of semi-solid-state batteries can be considerably reduced in the future.
After over 30 years, mass production of full solid-state batteries remains a distant reality. Solid-state batteries and their semi-solid-state counterparts are actually more different than their names might suggest. This distinction is necessary to avoid confusion regarding the practicality of mass-producing solid-state batteries, which has not progressed at the same rate as semi-solid-state batteries.
Lithium batteries can typically be divided into three categories: liquid, semi-solid-state, and full solid-state. As semi-solid-state batteries still utilize membranes and liquid electrolytes, their production methods are relatively similar to traditional lithium battery production processes, lowering their technical difficulty.
Full solid-state batteries are entirely different. “Compared to the current mainstream liquid batteries, from the four main materials (including positive and negative electrodes, membranes, and electrolytes) to battery assembly processes, and even to production equipment, changes may be needed (to accommodate the requirements of solid-state batteries), and all three aspects are indispensable,” said Wang.
Japan’s Toyota holds the most patents in the world in the field of solid-state batteries and has experimented with tens of thousands of electrolyte applications in batteries over the past 30 years. However, Toyota has yet to mass-produce solid-state batteries on a large scale, and the previously announced mass production timelines have been repeatedly delayed.
Multiple startups have also attempted to overcome this challenge one after another. According to the aforementioned investor, various startups operating solid-state battery projects have claimed that they can develop batteries with energy densities that surpass that of QS and Toyota. However, these indicators are often substantiated only by test data, with the prospect of integration into vehicles still dim.
While making small solid-state batteries in the laboratory is not difficult, and if factors like cycle life and charging rate are not brought into consideration, it is possible to manufacture batteries with energy densities of 500 Wh/kg or even higher. However, for commercialization, it is ultimately necessary to meet the six key aspects that influence battery performance: safety, energy density, cycle life, charging rate, temperature resistance, and battery management system (BMS) architecture.
“Some materials can be fashioned into small batteries with high energy densities, but it’s more problematic when making large battery cells with more layers. This is a common problem,” the investor said.
The recent breakthrough by QS in solid-state batteries has also been subject to skepticism among industry professionals. According to Volkswagen’s release, the test ostensibly proved that the solid-state battery from QS can achieve over 1,000 charging cycles with 95% or more capacity retained. Depending on the vehicle model, the company purported that an electric car could drive over 500,000 kilometers without any notable loss of range. However, these are ultimately theoretical, based on mathematical models, and assume ideal conditions during calculation.
In addition, Volkswagen publicly stated that the samples provided by QS are Type A. It is understood that the mass production of vehicle batteries needs to go through multiple stages: Type A is the test of individual battery cells, Type B is the test of battery packs after grouping batteries, and Type C is the test of performance when integrated into vehicles. Each stage requires at least more than a year to complete. This means that the solid-state batteries from QS are likely still far from mass production for vehicles.
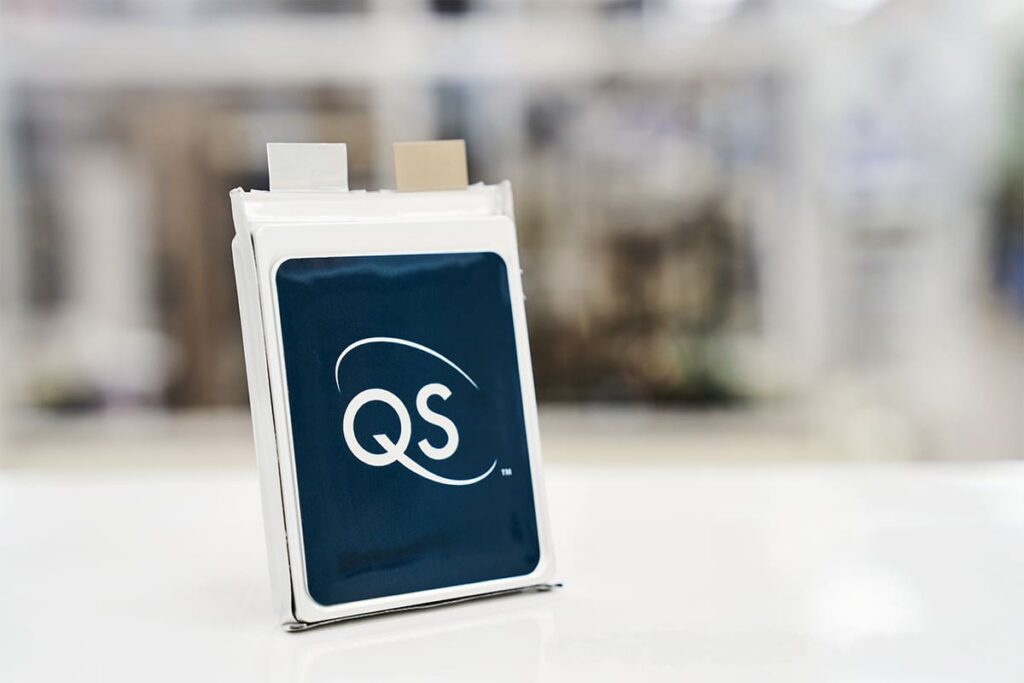
Even if breakthroughs are achieved in materials, equipment, and manufacturing processes, and full solid-state batteries can be widely applied, the thorny issue of cost competitiveness must be addressed.
For a long time, people’s expectations for solid-state batteries were to charge once and travel 700 kilometers. However, liquid batteries can easily achieve this goal now. This ultimately means that solid-state batteries can only be differentiated based on safety and energy density, enabling vehicles to achieve the same range while reducing volume and weight.
In terms of cost, solid-state batteries must also compete not with the liquid batteries of yesteryear but those of the upcoming years between 2025–2030, when the performance and cost structure of liquid batteries will continue to be optimized.
In recent years, leading solid-state battery manufacturers such as Toyota and QS have proposed mass production schedules, but all have ultimately delayed, pushing the promised mass production time further. The latest news is that Toyota revised the mass production time of full solid-state batteries again in November last year, postponing it to after 2030.
36Kr noted that mass production after 2030 is also the unanimous expectation of many industry experts. However, the phrase “after 2030” itself is vague and cannot be considered a clear timetable. This implies that full solid-state batteries are still far from commercialization.
“Toyota will probably repeatedly introduce a new five-year timeframe to achieve mass production every three years. In reality, talking about mass production in five years from now is basically equivalent to saying that the timetable is indefinitely shelved,” said Xu Xiaoming, general manager of Anchi New Energy Technology (ANC), at a recent conference.
This article was written by Wang Fangyu in chinese and was originally published by 36Kr.
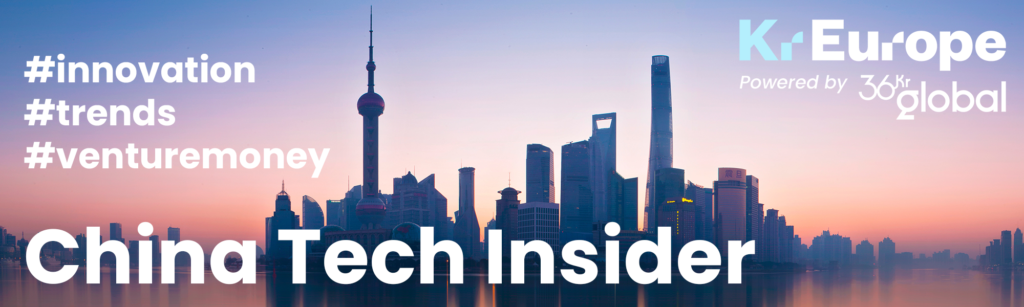